Refrigeration system
Refrigeration is the key link to achieve low-temperature simulation. Most environmental test chambers use a compression refrigeration system, and its working principle is based on the reverse Carnot cycle. The system is mainly composed of four core components: compressor, condenser, throttling device and evaporator. The compressor compresses the low-temperature and low-pressure refrigerant gas into a high-temperature and high-pressure gas, and then the high-temperature and high-pressure refrigerant gas enters the condenser, where it releases heat through heat exchange with the external environment, and the refrigerant gas gradually cools and liquefies. Then, the liquid refrigerant passes through the throttling device, the pressure drops sharply, and it becomes a low-temperature and low-pressure liquid, and finally enters the evaporator. In the evaporator, the low-temperature and low-pressure liquid refrigerant absorbs the heat in the test chamber and quickly evaporates into gas, thereby reducing the temperature in the test chamber. By controlling the operating frequency of the compressor, the flow rate of the refrigerant and other parameters, the low-temperature environment in the test chamber can be accurately adjusted.
Heating system
The heating system is used to achieve high temperature simulation. Common heating methods include electric heating wire heating and infrared heating. Taking electric heating wire heating as an example, when current passes through an electric heating wire with a large resistance, according to Joule’s law Q = I²Rt (where Q is heat, I is current, R is resistance, and t is time), the electric heating wire will generate a lot of heat. This heat is transferred to the air in the test chamber by heat conduction and heat convection, thereby increasing the temperature in the test chamber. By adjusting the voltage or current of the input electric heating wire, the heating power can be accurately controlled to achieve precise adjustment of the temperature in the test chamber.
Humidity simulation principle
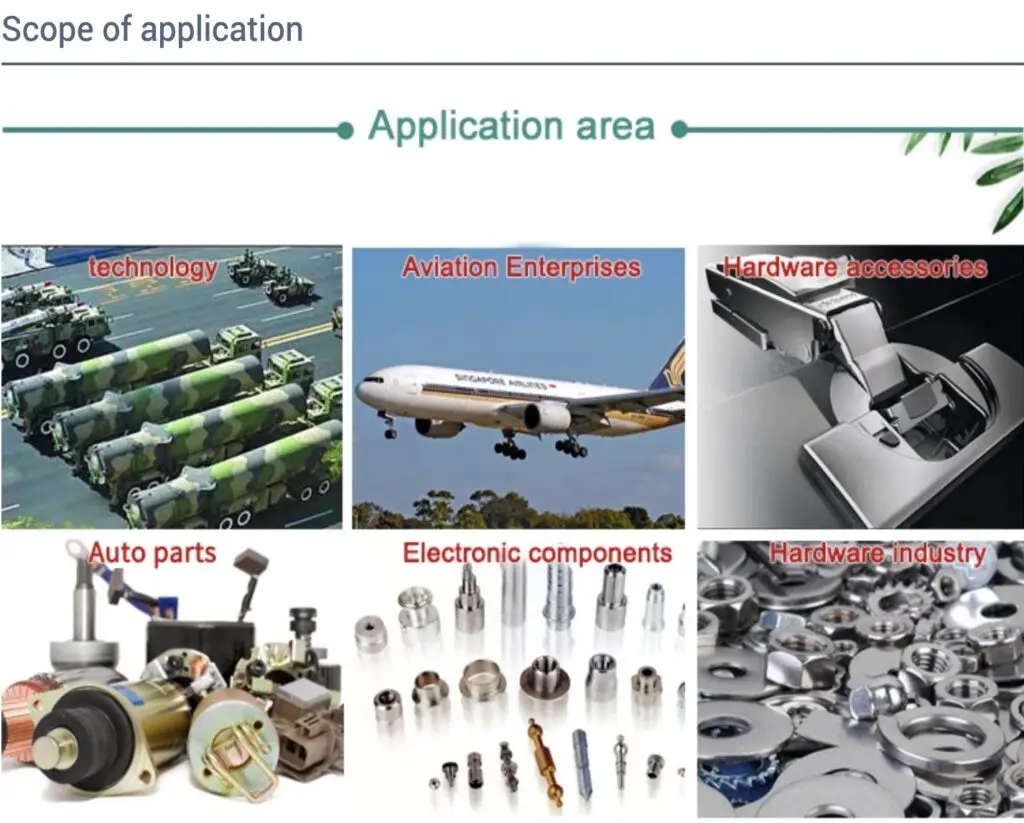
The humidification system is responsible for creating a high humidity environment in the test chamber. Common humidification methods include steam humidification and ultrasonic humidification. Steam humidification is to heat water to boiling, generate water vapor, and then introduce the water vapor into the test chamber. By controlling the heating power of water and the delivery amount of steam, the humidity in the test chamber can be accurately adjusted. Ultrasonic humidification uses an ultrasonic generator to generate high-frequency oscillations to atomize water into tiny water droplets, which evaporate rapidly in the test chamber, thereby increasing the humidity in the test chamber. Ultrasonic humidification has the advantages of fast humidification speed and uniform humidification, and can control humidity changes more accurately.
The dehumidification system is used to reduce the humidity in the test chamber. Common dehumidification methods include condensation dehumidification and molecular sieve dehumidification. The principle of condensation dehumidification is to use a refrigeration system to reduce the air temperature in the test chamber to below the dew point temperature, so that the water vapor in the air condenses into liquid water and is discharged through a drainage device, thereby reducing the air humidity. Molecular sieve dehumidification uses the adsorption characteristics of molecular sieves on water molecules. When humid air passes through an adsorption device equipped with molecular sieves, water molecules are adsorbed by the molecular sieves, thereby achieving air dehumidification. Molecular sieve dehumidification is suitable for test environments that have extremely high humidity requirements and require long-term stable dehumidification.